A Comprehensive Overview to Welding Assessment Techniques and Finest Practices for Quality Control in Fabrication Projects
Welding examination serves as a basic pillar in guaranteeing the architectural integrity and safety of made jobs. Developing efficient methods and a robust quality monitoring system can enhance conformity and reliability.
Value of Welding Evaluation
Welding inspection is an essential part in ensuring the honesty and safety and security of welded structures. The procedure includes a systematic assessment of welds to recognize any type of issues that may jeopardize the strength and longevity of the final item. Efficient examination is essential not only for conformity with sector requirements and guidelines but additionally for guarding the health and wellness of workers and the public.
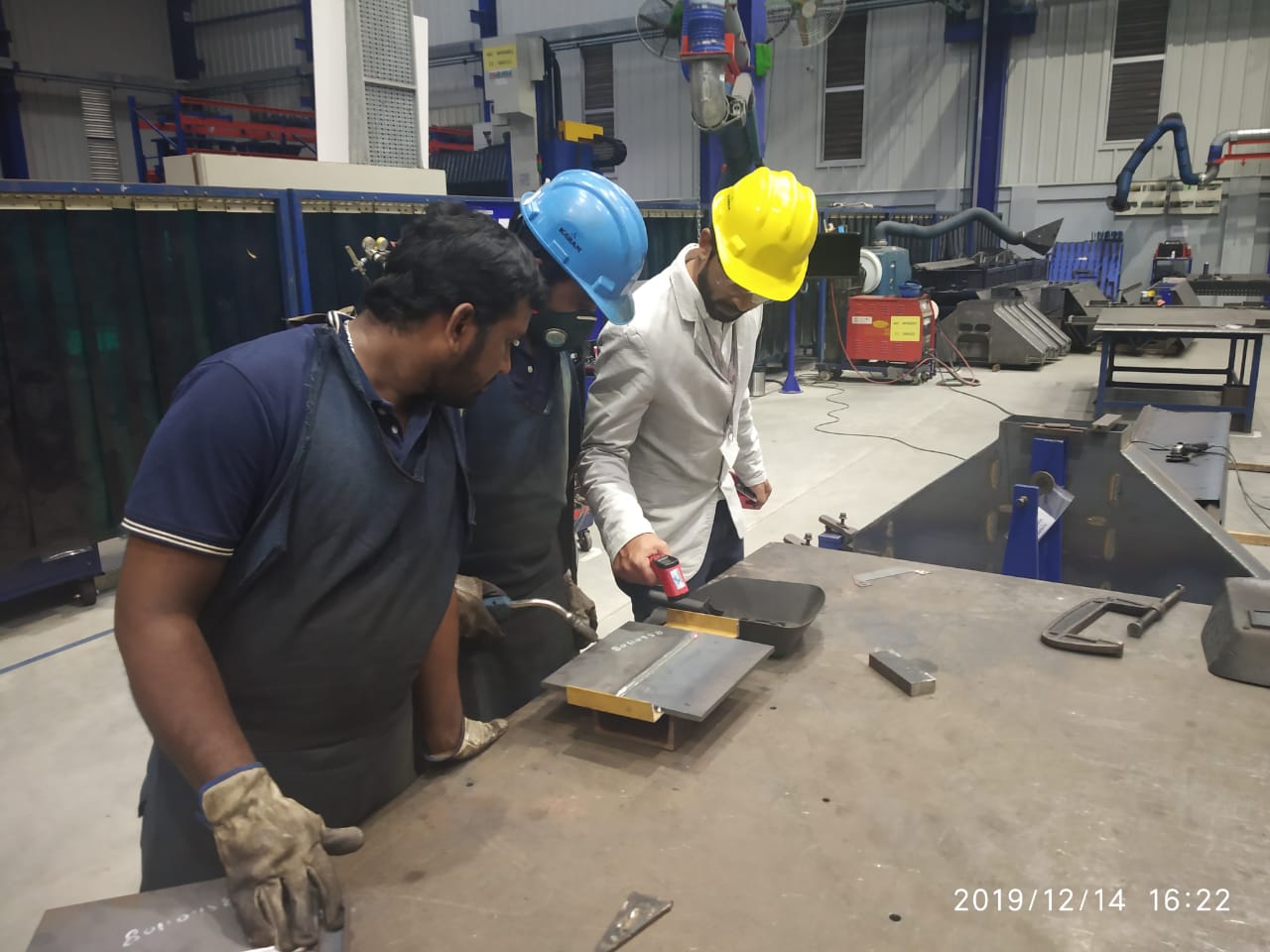
Additionally, welding evaluation acts as a useful tool for constant improvement in manufacture processes. By determining persisting issues, organizations can carry out restorative procedures, causing enhanced training for welders and better general techniques. Ultimately, focusing on welding assessment fosters a society of quality control, making certain that jobs fulfill both client expectations and regulatory demands. This proactive strategy is vital for achieving excellence in welding and manufacture.
Usual Welding Assessment Techniques
Numerous techniques are employed to examine welds, each customized to find particular kinds of issues and ensure high quality. Amongst the most frequently utilized techniques are visual inspection, ultrasonic testing, radiographic testing, magnetic fragment screening, and dye penetrant screening.
Visual assessment is the most simple technique, permitting inspectors to identify surface area abnormalities such as splits, porosity, and damaging. Ultrasonic testing uses high-frequency sound waves to identify internal flaws, offering an extensive assessment of weld stability. Radiographic testing utilizes X-rays or gamma rays to develop pictures of the weld, exposing interior defects that are not noticeable to the nude eye.
Magnetic bit screening is particularly efficient for ferromagnetic products, recognizing surface area and near-surface defects by using electromagnetic fields and utilizing great bits that indicate irregularities. Dye penetrant screening entails using a colored dye to the weld surface, which seeps right into fractures and is exposed under ultraviolet light, making it simple to spot defects.
Each of these strategies plays a critical function in keeping welding quality, and the choice of an ideal technique depends upon the certain needs of the manufacture job, including material type, weld arrangement, and the wanted degree of evaluation.
Vital Evaluation Tools

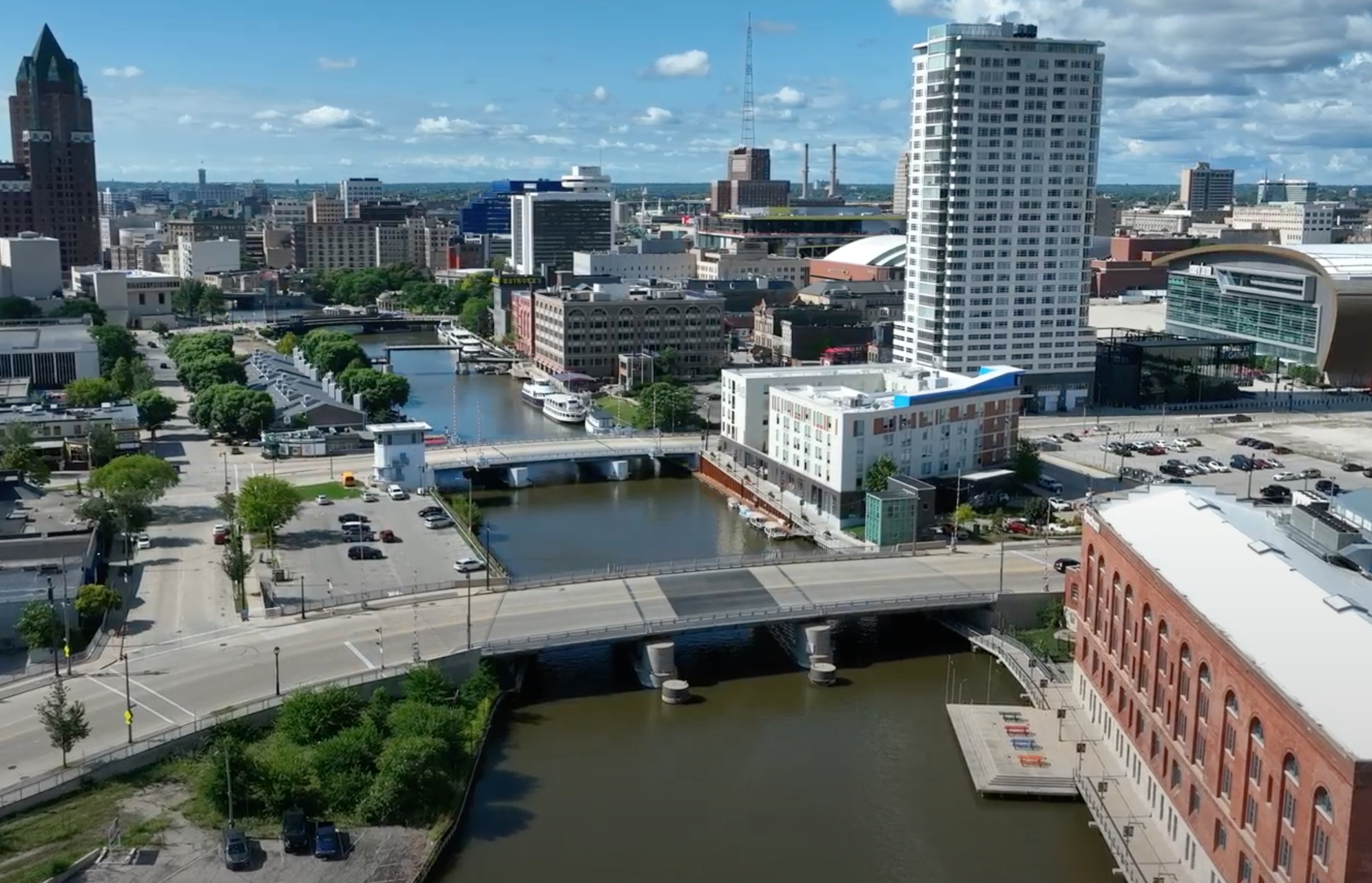
Measuring tools, including calipers, determines, and rulers, are important for validating measurements and pop over here tolerances. These tools help guarantee that welds satisfy the called for specifications for strength and toughness. In addition, ultrasonic testing devices are utilized to find internal defects without jeopardizing the stability of the weld. This non-destructive screening approach is crucial for identifying problems that may not show up on the surface.
An additional essential tool is the solidity tester, which assesses the mechanical residential or commercial properties of a weld and identifies its suitability for certain applications. Welding evaluation software application aids in recording searchings for, helping with information evaluation, and ensuring compliance with industry requirements. With each other, these vital assessment tools form an extensive arsenal that sustains the welding assessment process, inevitably adding to web link the high quality guarantee of fabrication tasks.
Finest Practices for Quality Guarantee
In the pursuit of quality control, implementing finest practices is crucial for accomplishing dependable and regular welding results. Establishing a detailed welding top quality monitoring system (WQMS) is basic. This system ought to encompass specified treatments, criteria, and paperwork methods that lead every stage of the welding procedure.
Normal training and accreditation of welding workers are vital. Competent welders with upgraded expertise of techniques and security measures contribute substantially to quality. Furthermore, performing pre-welding inspections guarantees that products and tools meet specified requirements, lowering the likelihood of problems.
Including real-time monitoring during the welding process enables prompt discovery of abnormalities, enabling restorative activities to be taken without delay. Post-welding inspections, including visual checks and non-destructive testing (NDT), are important in validating weld honesty and conformity with industry requirements.
In addition, keeping precise records of assessments, weld criteria, and corrective actions promotes a society of liability and continuous enhancement. Involving stakeholders in normal quality reviews can also enhance the total effectiveness of quality guarantee procedures. By sticking to these finest methods, companies can dramatically boost their welding quality control efforts, thereby ensuring project success and customer complete satisfaction.
Enhancing Safety and Conformity
Attaining high requirements in welding high quality assurance normally lines up with the critical of improving safety and conformity within the market. Effective welding examination strategies are important in identifying possible dangers and guaranteeing that all processes abide by regulative standards. These strategies not only offer to maintain architectural stability but additionally safeguard the health and wellness of personnel entailed in fabrication tasks.
Executing strenuous evaluation methods, such as visual exams, non-destructive testing (NDT), and complete documentation, develops a society of security and liability. Training welders and examiners in current security laws and best methods is important. This makes sure that all team members are mindful of potential dangers and are furnished to mitigate them.
Furthermore, conformity with sector standards, such as those set by the American Welding Society (AWS) and the International Organization for Standardization (ISO), like it is non-negotiable. Regular audits and evaluations assist recognize voids in safety measures and promote continuous enhancement - Welding Inspection Milwaukee. Eventually, a dedication to boosting safety and compliance not only fosters a safer working environment but also results in remarkable high quality results and lowered responsibility for companies engaged in welding manufacture
Final Thought
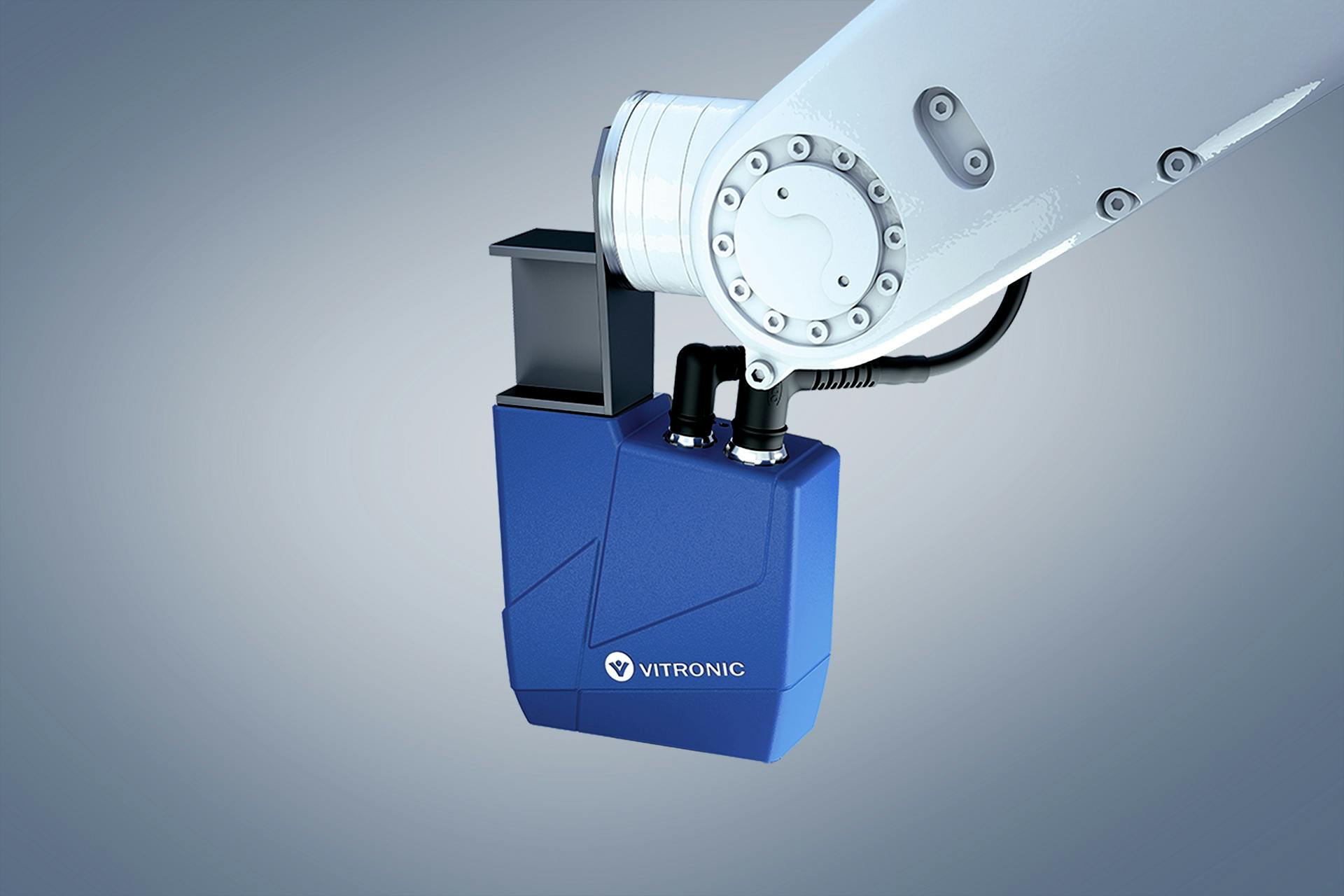
Welding inspection serves as a basic pillar in making sure the architectural integrity and safety and security of fabricated jobs.Welding examination is a critical part in making certain the honesty and security of welded structures. Eventually, prioritizing welding evaluation cultivates a society of quality assurance, making sure that tasks meet both customer expectations and regulative requirements. Together, these necessary examination tools form an extensive toolbox that sustains the welding assessment procedure, inevitably adding to the quality assurance of fabrication projects.
In conclusion, effective welding evaluation is necessary for making certain the architectural honesty and safety and security of made tasks. Welding Inspection Milwaukee.